This is the Auto World 4Gear Scooby Doo Mystery Machine HO Slot Car. These cars are compatible with Auto World, Tomy, and AFX tracks. Silver Screen Machines - Release 31 As part of the new Auto World Silver Screen Machines Release 31, these slot cars are replicas of the sensational vehicles seen in action on small and silver screens around the.
09/25/2011
Review
By
Eric Cropper
In the immortal words of Arnold, “I’m back.” I’m going to show you the ins and outs of the newest homebrewed tire truer available for our hobby, the Tire Razor. This product comes straight out of Missouri and is built by a one man operation that just started off to show folks that they could make a tire truer themselves if they had the right tools in their garage or basement. The Tire Razor prototype caught the eyes of many and soon its creator started getting asked, “How much to make me one?” Thus, began Jon’s effort to produce and sell a quality product with an exceptional price compared to similar machines already on the market. He isn’t just making these to make a buck off up groove riders, because he’s one himself. He has a passion for toys cars just like the rest of us and his efforts with the Tire Razor show it.
So, let’s grab that plastic case fresh car purchase or an oldie, but wobbly and get to the truth about this tire truing system.
VIEWING THE VARIOUS PARTS OF THE TIRE RAZOR
The Tire Razor is a beefy unit made out of 60-61 aircraft grade aluminum and it looks like it will last for years of use. The Razor comes with everything you need to start sanding your wheels and tires except for the wiring to connect it to your power supply. This allows you to wire it specifically for whatever brand or type of power supply you will be using to power it.
Personally, I only have my MG power supply located under the track table. I used about 10 feet of cable to give myself enough leash to comfortably use my Razor. The motor tabs accept 3/16” spade connectors and then use whatever best fits your power supply on the other end. I actually used ¼” spade connectors that I already had on hand and banana plugs on the supply end of my power leads. I just had to give the spade connectors a squeeze with a pair of pliers to make for a tight fit.
Oh yeah, upon removing your Tire Razor from the box and bubble wrap you will notice it’s already dirty with rubber. That’s Jon’s way of letting you know he’s tested your Tire Razor before it was shipped.
Note: I will be comparing the Tire Razor to the Area 3 several times within this review. This is only for comparison of two similar products and not to be taken as a bashing of the Area 3 product. I have only used these two machines and I find both to do what they are advertised to do. However, there are a couple of things about the Tire Razor that I personally think allow for a better experience while truing a set of wheels and tires. This is why I will be pointing them out to you.
Above are the loose parts of the Tire Razor system. You get an axle pulley, wrench for the set screws and 2 power bands. Also, to help you get sanding immediately Jon includes a couple of pieces of sandpaper.

The TR’s axle pulley is smaller in diameter VS the Area 3. It gives a bit more clearance when sanding small diameter wheels and tires. The band can end up hitting the insides of the channel cut into the sanding block if you go too far back and forth with it. The Razor can still do this too, but the smaller diameter pulley gives you a little more room when sanding smaller diameter wheels. However, you still need to use caution with both machines and this is in no way a deal breaker to purchase either machine.
Below is the sanding block which is a solid piece of material. Jon’s version has the channel offset. So, you have a good amount of stock to place you fingers upon to guide the block during sanding. This helps keep those much needed phalanges clear of the wheels and pulley during operation. The sand paper is the sticker backed paper and can easily be pulled up and replaced with a new piece. This type of paper is available at your local hardware store. FYI: Drywall sanding paper works great on silicone type tires.
Here’s a close-up of the axle forks for lack of a better term. The cutouts hold the axle bushings in place and allow the axle to spin freely under power. These forks are going nowhere if you are concerned with bending or warping. Unless, you plan on dropping or taking a hammer to it you’ll be pleased with its construction.
Above is a shot of the channel that holds the sanding block in place. As you can see there are 2 screw holes on the end and 1 on top at the far end too. What are they for? That’s for Part 2 of this review, but it involves plastic wheels, cutting and very little time to do it from what I’m told by Jon. Ok, you broke me down!!! These screw holes are for a separately bought lathe attachment. There, you happy now?
You can also see that the Tire Razor has foam rubber feet glued to the bottom of it. This greatly helps in keeping the unit planted upon the work surface. It doesn’t sound like much and anyone could add the feet themselves, but it is annoying when a tire truer starts to creep on you during use. This little detail just adds to the enjoyment of using this product.
Below, you can view the sanding block in its natural habitat. The channel and block fit together very well. There is no unnecessary drag involved when you slide the sanding block side to side within the channel.
Looking at the shot below, I will point out another difference between the Area 3 and the Tire Razor. Until I used the Razor, the only other tire and wheel truer I had used was my buddy Matt’s Area 3. We were really impressed with it and considered it worth every penny HE paid for it. LOL. However, the one thing we came to dislike about it was the fact that it only had one tension spring. The more it got used, the side without the spring ended up touched the sanding block less than the side with the spring. You couldn’t get both tires sanded at the same time. We had to sand one wheel or tire and then undo the power band, flip the axle and then true the second wheel or tire to get the job done. It still did the job but, it added more steps to get a finished product. It was more annoying than anything.
The Razor could develop the same issue down the road, but I think the spring strength will diminish more evenly since there are two springs VS just one. As for right now, both tires touch and get sanded at the same time.
I don’t know the specs on the Area 3 motor but, I can say that the TR motor is more than enough and maybe too much. The motor is rated for use in the range of 5 to 15 volts. I can’t imagine turning this thing up to 15 volts. Jon said it will throw the tires and I’ll take his word for it. I’d like to keep my eyes and teeth intact. It’s also suggested that if you power supply doesn’t have circuit protection that you add an inline fuse while wiring yours up. Supposedly, R/C battery packs have been used to power the Razor too. I have no idea on long these would last, but it gives you another option to try if you’re into that hobby in addition to our beloved slots.
Below, the motor pulley is made of the same material as the axle pulley and it’s also held in place with a set screw. You’ll want to check it for tightness before each use as an added precaution.
This is just a quick peek at the wiring configuration I did with my Tire Razor.
Finally, the bottom view of the unit. There is nothing that needs to be touched or adjusted under here. Those rubber feet I mentioned, also serve as clearance for the screws that the springs and such reside upon on the top side. They were added more for this need, but they still kill two birds with one stone.
THE SET-UP PROCESS
Above is the axle pulley. The left is when the set screw is in the secure position and the right when it is in the release position. It’s not pretty or as finished at the Area 3 but, it gets the job done and that’s all that matters to me.
Below, you see the pulley fixed onto the axle. You’ll want to get it as centered as possible on the axle and make sure to make it fairly tight. When doing a rear axle you’ll want to place the pulley up against the gear on the side opposite of the gear’s teeth.
The pulley is held snuggly in place by the set screw and is ready for action. So, grab the power band and put it over the pulley and hold it in place with your fingers.
Next, you’ll place the axle into the forks and with your spare hand reach through the rear opening of the tower to grab the back part of the power band. Now stretch the power band back over the motor pulley.
This is what it should look like below once the axle has been seated into the forks and the power band has been put into place.
Make sure the bushing are fully seated and centered into the cutouts. The tension of the band will keep everything in place. The final set up check it to make sure both the axle and motor pulleys are aligned with each other.
This is important for a smooth tracking axle during operation. You’ll want to keep the wheels from rubbing up against the bushings during operation as much as possible. Sometimes it just can’t be helped on shorter axle assemblies but, it is something you want to try and strive for before powering the machine up. This is needed more so with plastic wheels. The added drag can cause the wheel to become loose on the axle and in most instances the hole will be opened up and the rim made useless. The axle forks are an inch apart. So, for the most part it’s easy to avoid parts from rubbing against each other.
Above, you see a pretty well aligned drive train.
The picture above and below show an axle assembly that has been properly set up.
As I said above, it is very important to have the pulleys aligned up as close as possible to take any drag and possible angle of the power band out of the equation before starting to work on a set of wheels. This is another area where I think the Tire Razor rises above the Area 3. The motor mount can be loosened and the entire motor moved side to side for perfect alignment of the pulleys. The Area 3’s motor is stationary but, the motor pulley has 2 different grooves to place the band into to compensate for any misalignment of the pulleys. However, sometimes the 2 different grooves are just not enough to make up the difference based on my experience with the Area 3.
Simply unscrew the motor mount screws with a #4 hex driver. Move the motor to align the pulleys and retighten the screws. You don’t have to torque these screws too tight to lock down the motor bracket. I will warn you that the bracket also has some front to back play when loose. So, look down from above and align the edge of the bracket to the edge of the recessed area the motor resides in before tighten the screws. This will get you eyeball perfect.
This feature gives a lot of adjustability to the drive train for smoother operation.
The right tool for adjusting the motor mount.
The shot below is to just give you an idea on the amount of vertical movement that the Tire Razor has to offer. Personally, I don’t see myself needing to ever use all of it, but it’s good to know you have it available if you do need it. You can actually take it lower than what I show here, but why stress out the springs any more than I have too.
The above shot shows the distance between the wheel and the sanding block with the tower in its utmost position. It took about a full turn of the knob to make contact with the sand paper. This isn’t going to be the case with each and every tire, but the point is to take it slow. Patience!!!
SANDING THE RIMS AND TIRES
I’ll be using my recently acquired Supra’s rear axle for this demo because they’re white and it will be easier to see the progression during the sanding process. The first thing is to get the axle mounted and the drive band aligned as described above. It’s a tight fit with a NINCO angle winder set up, but it has enough clearance between the axle fork and the gear. Just be cautious before powering it up.
The MOST IMPORTANT step before you start the true anything is to make sure the bushings are oiled. DO NOT run the machine with an axle set up that hasn’t been properly lubed.
The next tip you can do or not do depending on your opinion of it. It doesn’t really work on dark colored rims, but on silver and lighter colored rims it really helps a person know how the sanding of the rib is progressing under power. Start up the Tire Razor and grab a dark colored Sharpie or other type marker and run the marker across the rim rib to color it. Why? Under power it’s hard to tell when you’ve finished without turning the machine off and on repeatedly to check your progress. This trick lets you know when the rim is perfectly trued. You’re done when all the color from the marker is gone.
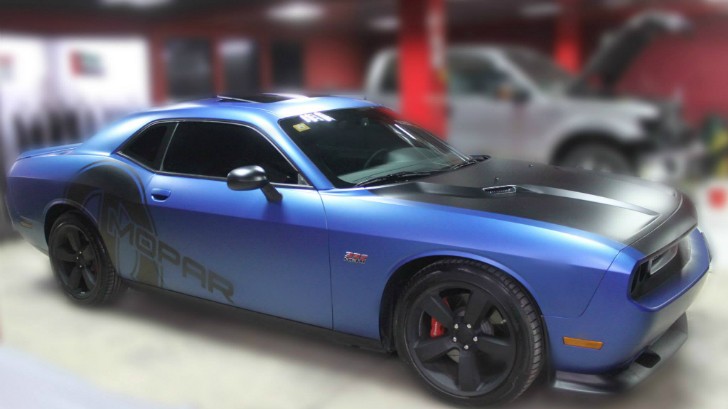
Below is what you will end up with after running the marker across the rib of the wheel.
When you begin sanding the wheel and/or tire you want to take your time. Turn the knob to lower the axle a little bit at a time. If you go cranking the knob like a gorilla, you’ll risk ruining your plastic wheels. This motor has a lot of torque and if you bog the wheels down by putting too much pressure on them the axle will spin within the hub and open up the hole in the hub. It will happen before you can react too. Take it easy and take it slow or you’ll be kicking yourself in the butt.
Step #1
You can see that the marker is starting to disappear as the plastic wheel is starting to become true.
Step #2
We’re almost there. There is just a small amount of marker left on the outside edge of the rib.
Step #3
They’re done. So, how long did it take? No more than 3 or 4 minutes and remember I was stopping to take pictures too. This doesn’t mean this is the time for all types and brand of wheels. I’ve spent longer doing badly molded wheels. The worst ones I’ve done were the front wheels of a Sloter Lola. This was with Matt’s Area 3 and afterwards it was smooth as glass. Prior to using a truing machine on them, it bounced like a low rider with switches. It took a while to get them done because they were so bad that I had to constantly check them for tire fit. The one thing you need to remember is if you go too far, there’s no going back in the other direction. Take your time. I can’t stress this point enough.
Now that you have the wheels trued you are ready for the tires. Go ahead and put the tires on the newly trued wheels and put everything back into position. Now just repeat the same process as you did with the wheels on the tires. You’ll want to make sure to use even more patience now since the tires will take more power to reduce the drag that they make on the sandpaper. Since you can’t do the marker trick you’ll have to start and stop the machine to view you progress. You’ll want to do this to give the tires a break from the constant fiction of the sandpaper and allow them to cool down too. Don’t over heat your tires. This will cause them to become loose upon the rim and risk spinning them off the wheel under power.
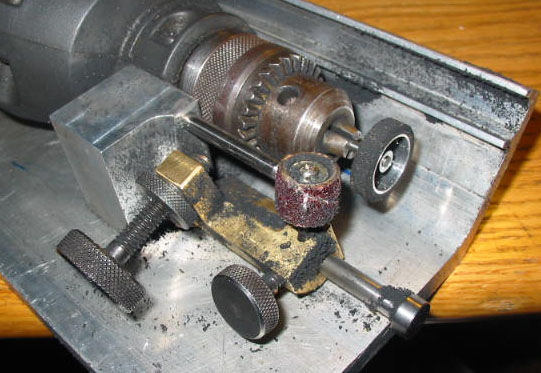
The video isn’t of great quality. Sorry, but my camera just can’t focus in video mode that close. However, you will hear the bog of the tires touching the sandpaper as I turn the knob and this is when you want to stop turning and work the sanding block back and forth before turning the knob any further. Basically, you just repeat the process until you are satisfied with the results. A truing machine also makes rounding the edges of a tires an easy task too. You can use the sanding paper, the sanding block or a nail file like we do to accomplish it. Just take special care not to hit your gear with either of these items.
Below, I overexposed the photo so you can see the progress of the sanding of the tires. The shiny area on the right side tire indicates that the outside edges are still higher than the middle of the tire. So, keep sanding.
The aftermath of a truing session. Each and every rim and tire is different. Sometimes you’ll have very little mess and other times it will look like you left no tire on the rim.
Now take your newly trued tires and run them across some tape to remove the residue left behind from sanding them. After this step clean the tire with lighter fluid or whatever your weapon of choice is for this task.
Yep, there’s more than you think there will be at times. It all depends on the type of tire you are truing. Believe it or not, the tires still were not clean after the tape. Even more came off with the lighter fluid.
JUDGMENT DAY
I know everyone doesn’t have the funds to buy a tire truer not matter who makes or sells it. However, I approached Jon about doing a review partly because I thought his machine would be well received by the folks on HRW. I know that when the Area 3 came out, the common statement was, “It’s too expensive for me!” and “Does it really work that good?” It took several folks dropping around $250 to find out that in fact it was worth it. They posted their experiences with it (including myself) and the news spread and caused several others to save and buy one themselves. I’m simply trying to do the same with the Tire Razor with this review.
This is where I will compare the Tire Razor to the Area 3 for the last time in this review. The price!!! You get everything I showed you in this review for around $150 shipped. This adds up to about 3 Slot It cars instead of 5 to get the Area 3. When it comes to people making hard decisions on what to spend their hobby funds upon, this $100 difference is a substantial savings to the consumer. I think it’s a price more folks can stomach and rationalize when it comes to making such an investment in a product such as a tire truer.
If you are in the market or on the fence about buying a tire truer I hope I provided enough information about the Tire Razor for you to consider it as the weapon of choice. It’s a quality machine that gets the job done like the others on the market and you can’t beat the price.
Now for the bad news. Jon (aka scrjon) is a one man operation. He is currently working with a shop to make some of the parts for him to free up more time for him to make the other parts needed and time for assembly. However, he makes them as he sells them. He tries to keep several in stock, but if 10 people contact him about buying one after this review, he’s not going to have 10 to sell. He’s a machinist by trade and is doing the Tire Razor in between work and life in general. So, you may have to wait for yours to be built. The question is, “Is the added wait worth an extra $100 in your pocket?” Only you can answer that question, but I know how my wallet would answer.
Feel free to contact me with any additional questions or concerns about this review and a big THANKS to Jon for supplying me the Tire Razor for this review.
Eric Croper
AKA Legionofone
Tire Razor Part 2
The Lathe
By
Eric Cropper
This is the second installment of the Tire Razor product line.
If you didn’t see theoriginal review of the Tire Razor you can find it here.
If you purchased a Razor, you’ve probably already spent hours getting the wheels and tires of your slot fleet trued to perfection. Maybe, you just got a box in the mail with a couple of new rides that need some Razor TLC. Then the Razor sits until the arrival of its next victim.
Maybe, it doesn’t have too.
Do you use after market metal wheels?
Did you scratch build that perfect car from a model kit?
Tired of your press-fit plastic wheels coming off during a race?
Got a stock plastic wheel that has a broken hub that can’t be repaired?
The Tire Razor Lathe might be for you if you answered yes to any or all of these questions.
The title shot above gives you an overall peek at the Lathe and all that comes with it. It’s made out of the same aircraft grade aluminum as the Tire Razor and is another handmade product. So, again remember that there might be a wait if and when you decide to order one for yourself. Time for a closer look…
360 Look of the Lathe
Above is the control knob for the side to side axis that moves the bed of the cutter. A nice textured knob to prevent finger slips and added control for fine movements.
Below is the front of the cutter. This is the side of the lathe that faces the wheel you’re cutting down. I’ll cover the various screws and their functions later in the review. Yes, it’s dirty. I took the pictures after using it. Also, yours will arrive dirty just like your Tire Razor. Jon personally tests each item he makes before it is shipped to its new owner.
Below is a different view of the front side of the lathe and in the foreground you can see the side mounting bracket.
Above is the backside of the cutter and the threaded black knob controls the forward and reverse of the cutter base.
This concludes the 10 cent tour. You now ask, “How does this thing mount to my Razor?” It’s as simple as 1-2-3.
Mounting System
Above is 1-2-3. #1 is the slide mount bolt for lack of a better term. #2 and #3 are your side mounting bracket screws.
The order that you use these to mount your lathe isn’t important, but below is how I do it.
The lathe simply fits in the channel where the Tire Razor’s sanding block usually resides. You will see the bolt hole on the right side of the channel. This is where the slider mounting bolt is used to hold the bed of the cutter in place. Slide the lathe into the channel and screw the bolt into this hole through the opening of the lathe bed. This bolt has an opening to use a #4 Hex Driver. However, you don’t need it when you install this bolt. You just want to hand tighten the bolt and you want it just tight enough to help keep the bed of the lathe in the channel of the Razor.
Next, we are installing the side mounting bracket with screws #2 and #3. Hold the bracket to align the holes in the bracket with the screw holes in the side of the Razor. Start the screws by hand to avoid cross-threading. Once you get them started you can switch to a #2 Hex Driver to finish the job and snug up the screws against the side of the Razor. Snug is all you need. So, don’t over tighten these screws. NOTE: You might have to mess with the position of the large knob control to get your hex driver in place for these screws.
Below is the fully mounted lathe attachment on the Tire Razor. I told you it was easy. This view gives you a better idea of how it all works. The large control knob on the left of the picture moves the lathe bed and mounted cutter side to side just as you would move the sanding block side to side with your hand. The black control knob moves the cutter base forward to cut the wheel and backwards to your starting position.
The Cutter
The pictures above show the range of movement for the cutter base. As you turn the black control knob, the threads turn through the cutter base mounting bracket located on the front with the 2 Philip screws in the photos above. NOTE: There is no need to mess with these Philip screws. There’s a large amount of distance front to back, but I doubt you’ll ever come close to needing it.
Below is a series of photos showing how to remove the cutting blade. The 2 set-screws on top of the cutter base accept a .050 Hex Driver. You don’t have to completely remove them in order to remove the cutting tool. Simply, do the reverse to install the cutting tool. Don’t over tighten.
The cutter base can also be removed from the lathe and repositioned to cut down larger width wheels. The screw used to remove and mount the base requires additional use of the #2 Hex Driver. The screw hole on top of the small rectangle section in the bottom right is the 2nd mounting position for wider wheels.
This shot shows the cutter base in the 2nd mounting position. I’d guess you gain around a quarter of an inch of clearance in this position.
Above are the cutting tools. I say tools because this is actually a 3 in 1 cutting tool. The left side in the photo is what Jon called a separating tool.
Slot Car Tire Truing Machine
The right side, depending on how you rotate and mount the cutter, is either a right or left handed cutter.
Below with the cutter base removed there is a mounting slot for another tool to be used with the lathe. A small saw blade is also included and can be mounted in the groove pictured below and held in place with 2 set-screws. They are the same .050 Hex Driver set-screws used to hold the cutting tool in place. This saw can be use to cut the face off of the turned down wheel to create the wheel insert. Although, looking at the picture I’d say it should be mounted with the angled bottom section between the screws. That would give you a better angle to cut the face of the wheel off. Honestly, Matt just grabbed a utility knife and cut it off by hand. However, if you don’t feel comfortable using a knife, this would be the way to go.
Prep Time
If you are cutting down wheels mounted on a knurled axel, such as, Carrera and Scalextric there’s no prep time before you start cutting down the wheel. However, if you are cutting down a wheel that is press fitted on a smooth axel, such as, Ninco or in my case Powerslot, you will need to glue the wheel onto the axel. We actually had to stop and glue the wheel two more times during the cutting process.
I suggest that you use an axel stop if you can remove a wheel to fit it on the axel. When it’s locked into place against one of the bushings it will help keep the axel assembly from moving side to side when the cutting tool is cutting into the wheel. We didn’t originally use one. You will see in one of the videos that the axel is moving with the cutting tool and Matt pushes on the wheel with his finger to finish the cut across the wheel. DON’T DO THIS…LOL. You’ll hear Matt say, “That’s rough on the finger.” (shaking my head)
Okay, now mount the axel assembly into the Tire Razor’s brackets as shown in the Tire Razor review. Remember to LUBE the axel bushings before you turn on your Razor. This is a very important step whether you’re just truing your wheels and tires or using the lathe.
Let the Plastic Fly
Okay, I’ve told you what knobs control what and that you can cut left or right. What else do you need to know, right? Turn up the power!!! We started at 6V and that wasn’t cutting it. If the tip of the cutting tool dug in too quickly it broke the glue bond and the wheel was spinning on the axel. We took it all the way up to 8V and eventually settled on 12V.
Now what? I wish I had a definitive answer for you, but I don’t. It’s a trial and error process to get the feel for the lathe. How much do I take the cutting tool forward? How fast or slow do I turn the horizontal control knob? It will be up to you to figure that all out. All I can say is turn the power on, turn the black knob slowly until you hear and/or feel the cutting tip against the wheel and now start turning the large silver (horizontal movement) control knob until you’ve cut across the whole width of the wheel. Repeat and repeat and cuss when you go too far and break the glue bond and glue it again and let it dry and repeat and repeat. See the pattern? LOL.
Here are 3 videos that show different stages of the cut down process.
CLICK FOR VIDEO 1You will have made a mess by the time you’re done. This is just from 1 wheel. Can you imagine the aftermath of 4 wheels? However, you don’t want to keep turning down wheels without cleaning in between each use. You will find that the plastic shavings can end up in places that can cause binding of the moving parts of the lathe. So clean it regularly.
The easiest way to clean off the Tire Razor is to use a can of compressed air to spray off all the debris. If you can spend the money on a can I suggest you do it. The plastic shavings can be a pain to brush or wipe away and you can use the air while the Razor is still under power. This can also be helpful when truing wheels and tires.
I can tell you one hint that will cut your cutting time and effort by 1/3. Review the picture below.
Above you have the complete wheel (top), the almost finished insert after it was cut off (left) and the piece at the bottom is the amount of the wheel cut off on the backside of the wheel. Matt used the utility knife to do this, but as I mentioned before you could use the saw blade included with the lathe to accomplish this task. This is the 1/3 less cutting I was talking about once it’s cut away from the backside of the wheel.
Here is the wheel cut down to the diameter of a SCX Pro Wheel. We actually took it a tad too far and a dab of glue would solve this issue. However, if you have a pair of calipers to gauge where to stop, it would be a great help. If not, then you just have to stop and see if you can slide the wheel over the end of the insert before cutting it off. Check often once you start to get close to the right diameter. If you go too far, there’s no turning back.
Here’s the insert sitting in the SCX wheel. The next steps are sanding and drilling the back of the insert until I reach the desired mounting depth within the wheel. The ending diameter of the insert is pretty close to the inside of the SCX wheel.
Observations
Looking at the lathe I can see that it’s probably a pain in the #@% to build and that it’s made of the same quality materials as the Tire Razor. I found myself thinking, “This is insane and overkill.” The only inserts I’ve ever made where from 1/24 models for a couple of H&R Racing chassis’ I’ve done in the past. I sanded them slowly by hand until they fit just right. A tool like this could have cut a 2 hour ordeal down to 20 minutes. I still don’t know how much I will use it, but I see myself lending it to Matt to use for his new found love of scratch building cars. I’m just not in that frame of mind with the hobby and either is my wallet.
I can use it on stock plastic wheels to true up the sides of that wheel that has extra material and causes the edges of the tire to sit higher than the middle of the tire. Yes, it will work for that use too.
Matt thought it did its job and he recalled sanding down 3 sets of 4 wheels for his 3 SCX Abarths with his Area 3. The hardest part with sanding a plastic wheel down is controlling the heat level of the plastic. You go too fast and hard and the plastic melts. Matt quickly pointed out, “There’s no heat doing it this way.” The 12 wheels took him forever to sand down to size when he replaced the stock wheels with some Ranch Design aftermarket wheels. “It works,” he says at the end of one of the videos.
Here are some callouts Matt and myself discussed and feel deserve to be mentioned about the lathe.
1.It’s handmade and very well, but it’s not going to beat an actual lathe. Keep this in mind.
2.The black control knob is so close to the working parts that it’s awkward to operate with big fingers. Extending the knob further out would be more comfortable to the user.
3.The need for multiple sized Hex Drivers to make all the adjustments to the lathe. If you don’t have them you will have to buy them.
4.You need a Tire Razor to use it. Ambitious folks might be able to adapt the lathe to another brand truer. (shrug)
5.Backlash and play within the cutter base. It affects the cutting of the wheel a bit once you start to apply the pressure of the tip to the wheel.
Will it get worse the more that you use it? I can’t answer that question. The video below shows the movement:
Judgment Day
The Tire Razor lathe attachment is well made for a guy designing and building it in his spare time. There’s no doubt about that fact. I know I don’t have the tools or knowledge to make it. If you already have a Razor and want something to cut wheels down to make custom or more period specific wheels for your slot projects, you’ll likely be satisfied with this lathe. It’s a space saver compared to a full blown lathe purchase, but you’ll be more limited for uses versus the real thing. It beats sanding down plastic wheels with just a tire truer and doesn’t create heat which is plastic’s #1 enemy. The cost of $85 is reasonable for a product such as this attachment. Your prayers may be answered If you’re tired of being limited to existing wheel inserts in the slot car market. If you have that old rare model kit to convert over to a running car and it HAS TO HAVE the original model’s wheel on it to look right…problem solved.
I thank Jon (scrjon) for supplying the Tire Razor Lathe for review and I hope I’ve given a fair and informative review to help you make a decision on purchasing the lathe and/or the Tire Razor with this 2 Part Review. Feel free to contact me with any questions and I will do my best to answer them.
Slot Car Tires Type Rubber
Eric Crooper
Slot Car Tire Truing Machine
AKA Legionofone